Short description of the "gene
of safety" - the device of thermal control over rotational elements
of the aircraft engine during the flight
Inasmuch as aircraft crashes become more frequent,
the problem of the safety of flying grows overwhelmingly important.
The problem is burning for aviation of any country.
The most commonly happening accident which
leads to the catastrophe in the air (airplane, jet aircraft, helicopter)
is a breakage of the aircraft engine that results in the dangerous
heating of the engine. The overheat broken-down engine is characterized
by unpredictable behavior: it jams, catches fire or even bursts up.
Modern methods of thermal control of rotational
elements of the engine (for instance, turbine blades) are based on
the use of microthermocouple with mercury contacts. This procedure
is helpful only for checking the engine functioning in the steady
state, i.e. during test installations on the ground. No control of
the engine temperature during the flight! Pilots do not posses any
information on the temperature of aircraft engine in the course of
the flight. Thus there exists a very important problem to exercise
a persistent reliable thermal control over rotational elements of
the aircraft engine during the flight.
We propose a system for the thermal controlling
the engine rotational elements in the structure of airborne equipment.
In this case the pilot can monitor the reading of the corresponding
scale and in the case of emergency the defective engine will immediately
be switched off. The device can be elaborated on the basis of infrared
detector having no direct contact with engine elements. The detector
will register changes in thermal radiation of the engine's rotational
elements, and then the signal will pass through an electronic block
of data handling and go to the airborne equipment. For example, a
temperature change in the turbine blades from 300 K to 1300 K should
give a change in the thermal radiation flux from 50 to 104
W/m2. At the output of the detector we obtain the signal
of the thermal flux that will significantly prevail over the noise
amplitude from 102 to 105. The problem is very
complicated by the sensitivity of the detector to vibrations and acoustic
influences. This is just what takes place in the aircraft: while the
motor is running, the level of noise is enormous and acoustic influences
reach 120 phon. But we can apply a special recompense procedure, which
will control the noise, - we have had already enough experience in
removing the heavy acoustic influence.
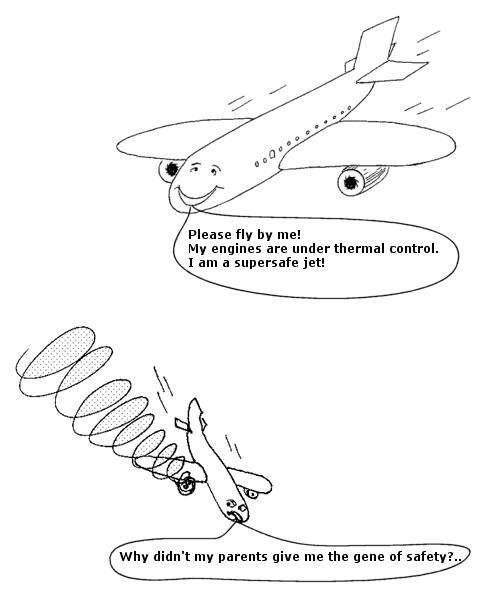